2024. 9. 12. 11:36ㆍ배터리/전고체 배터리 (All Solid State Battery)
고체 전해질 분리막 제조
고체 전해질 분리막을 제조하는 것은 기존에 LIB에 없던 완전히 새로운 생산 방법이라고 할 수 있습니다. 고체 전해질 중 오늘날 대규모로 생산되는 유일한 고체전해질은 폴리머 고체 전해질입니다. 무기 고체 전해질인 산화물과 황화물의 경우 현재 소규모 생산 라인과 실험실에서만 제조되고 있습니다.
일반적으로 논의되고 있는 고체전해질의 세 가지 제조방법은 습식, 건식, 분말기반 가공입니다.
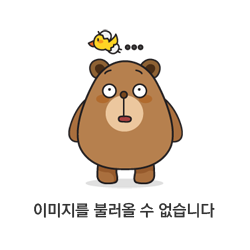
습식 공정
습식 가공 방법의 첫 번째 단계는 고체전해질, 바인더, 첨가제 및 용매를 슬러리로 혼합하는 것입니다. 황화물 및 산화물 고체 전해질의 경우, 물과의 반응성 때문에 물을 기반으로 하는 공정은 불가능하므로 유기 용매가 사용됩니다. 황화물의 경우 NMP와 같은 극성 유기 용매에 반응하기 때문에 용매와 바인더의 선택이 제한적입니다.
폴리머 및 폴리머-산화물을 혼합하는 복합체의 경우, 아세토니트릴이 종종 용매로 사용됩니다. 아세토니트릴은 폴리에틸렌 옥사이드(PEO)를 용해할 수 있고, 낮은 끓는점을 가지며 LLZO와 같은 대부분의 무기 입자에 대해 안정적이기 때문입니다. 마찬가지로, 황화물 고체전해질의 생산을 위해서는 자일렌이 종종 용매로 사용되며, 스타이렌-부타디엔 고무(SBR) 및 실리콘 고무(SR)와 같은 바인더와 함께 사용됩니다. 한편으로는, 고체전해질 분리막의 바인더 양이 너무 많으면 이온 전도도가 낮아지므로 최소화해야 하지만, 반면에 바인더 양이 불충분하면 고분자 전해질 입자의 상호 연결성이 부족해져 이온 전도도와 고분자 전해질 분리막의 안정성을 떨어뜨릴 수 있습니다.
고체전해질 분리막을 셀에 조립하기 위해, 이를 직접적으로 양극 위에 접착시키거나, 기존 LIB의 방식처럼 고체전해질 분리막을 따로 제조한 후 양극 음극과 적층 할 수도 있습니다.
고체 전해질 슬러리를 전극 위에 코팅하는 방법으로는 슬러리 캐스팅, 테이프 캐스팅, 스크린 프린팅 기술이 있습니다
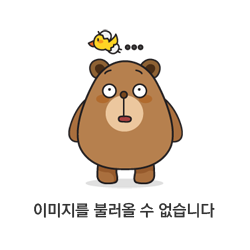
고체 전해질 분리막을 따로 필름으로 제작하는 경우 기계적 완전성을 보장하기 위해 일정한 두께(>30 μm)가 필요합니다. 반면에 고체 전해질 분리막을 전극에 코팅하는 경우, 매우 얇은 층(5-10 μm)을 얻을 수 있습니다. 높은 에너지 밀도를 가진 배터리를 만들기 위해서는 고체 전해질 분리막이 얇아야 하므로 LIB에서 사용하는 분리막과 유사한 두께(10-20 μm)를 가져야 합니다. 밀도가 높고 이온 전도도가 낮은 산화물 고체전해질을 분리막으로 사용하는 경우에는 더 얇은 두께를 가져야 합니다. 이러한 사실들을 고려할 때, 독립적으로 고체 전해질 분리막을 제조 후 전극과 조립하는 것보다 전극 위에 고체 전해질 분리막을 직접 코팅하는 것이 더 유리합니다.
마지막 단계는 층을 압축하는 과정으로, 형성된 SE 분리막 층을 캘린더링이나 프레싱을 통해 압력을 가하거나 고온에서 소결 (Sintering)을 통해 밀도를 높여, 전극과의 좋은 접촉, 낮은 다공성, 높은 이온 전도성을 보장합니다.
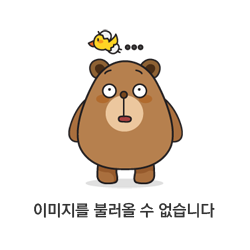
고분자 전해질은 높은 유연성 덕분에 캘린더링이 가능하며, 대부분의 황화물도 연성이 있어 캘린더링으로 밀도를 높일 수 있어, 산화물 전해질에 비해 생산 측면에서 이점이 있습니다. 대부분의 산화물 재료는 가공성이 없기 때문에 프레싱만으로는 충분히 압축할 수 없으며, 따라서 추가로 고온 소결 공정이 필요합니다.
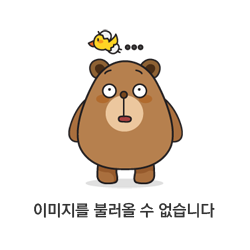
이 과정은 매우 조밀한 층을 만들고, 적은 결정립 경계를 가지며 높은 이온 전도성을 제공합니다. 그러나 소결은 매우 에너지 집약적이어서 비용이 많이 듭니다.
고체 전해질 분리막을 제조한 후 양극과 조립하는 경우 2단계의 소결 과정을 거치게 됩니다. 양극 활물질은 고온 소결을 견딜 수 없기 때문에 첫 번째 소결 단계에서는 고체 전해질의 밀도를 높이기 위해 가장 높은 온도를 사용하여 소결 하고, 두 번째 소결 단계에서는 SE 분리막을 양극 복합 전극과 결합하기 위해 온도를 낮춘 상태로 소결을 진행합니다. 소결 공정은 시간이 많이 소요되므로 생산 속도를 크게 늦추고 처리량을 제한하게 되며 리튬의 높은 증기압으로 인해 소결 과정에서 일정량의 리튬이 손실되므로 Li2CO3 형태의 과잉 리튬을 추가하는 것이 필요합니다.
산화물 분리막은 고체 전해질 분리막으로서 매우 유망한 특성을 보이기 때문에 소결 과정을 용이하게 하려는 많은 시도가 이루어지고 있습니다. 예를 들어, 소결 온도를 낮추기 위해 Al2O3와 Li3BO3와 같은 소결제를 추가하기도 하며 불활성 분위기에서 주울 가열 (Joule heating)을 사용하여 소결 시간을 1분 미만으로 줄이는 초고속 고온 소결 ( UHS: ultrafast high-temperature sintering) 을 하기도 합니다.
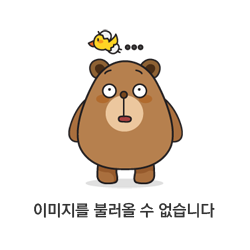
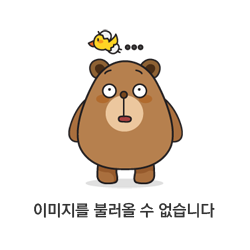
고분자 고체전해질도 습식 공정으로 처리할 수 있지만, 건식 압출 공정이 이미 확립되어 있고 더 비용 효율적이기 때문에 고분자 고체 잔해질에 습식 생산 공정이 적용될 가능성은 낮아 보입니다. 반면에 무기 고체 전해질을 양산하는 경우 습식 처리 방법이 더 유망합니다. 그러나 습식 생산 방식을 사용하는 경우 일부 산화물 및 황화물 고체전해질이 물과 반응하는 문제를 해결해야 합니다. 이를 위해 무기 고체전해질은 모두 건조한 환경에서 처리해야 하며, 특히 황화물의 경우 낮은 이슬점의 매우 건조한 분위기를 사용해야 합니다. 일반적으로, 습식 생산 공정은 현재의 LIB 생산 방식을 대부분 적용될 수 있다는 큰 장점이 있고 소결 공정을 적용하지 않을 경우 생산 속도를 높일 수 있습니다. 고체전해질 분리막의 습식 공정은 양극 복합체 생산과 유사하지만, 용매 회수 및 필름 건조공정이 복잡하고 비용이 많이 드는 문제도 존재합니다.
고체전해질 제조방법의 장,단점과 해결 과제
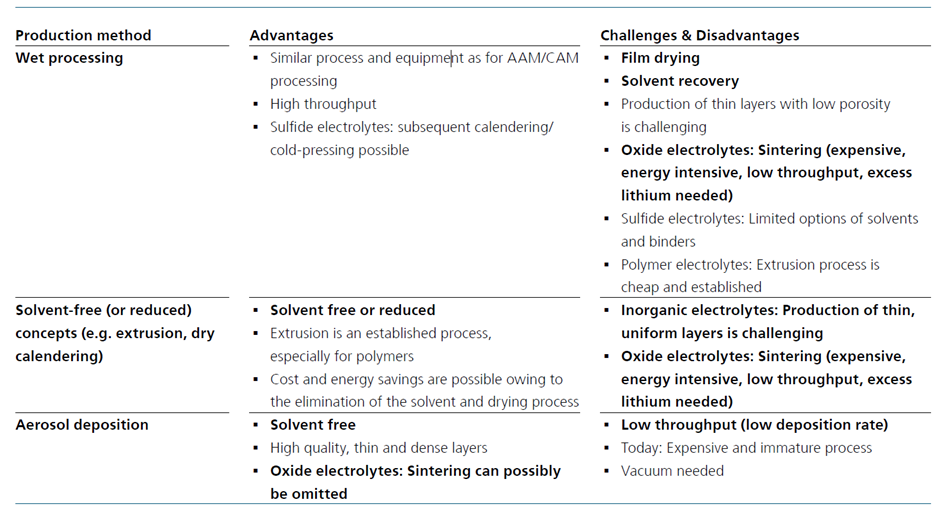
건식 공정
용매 회수 및 필름 건조에 드는 높은 비용을 줄이거나 완전히 없애기 위한 시도로, 용매를 사용하지 않거나 적은 양의 용매를 사용하는 공정이 활발히 연구되고 있습니다. 고분자 고체 전해질의 경우, 건식 압출 공정이 이미 확립되었습니다. 고분자와 리튬염을 혼합기에 균일하게 혼합된 후, 그 혼합물을 양극 복합 전극에 라미네이팅합니다. 그 후 캘린더링을 통해 고체 전해질 분리막의 밀도가 높아지고 전극과의 접촉을 향상시킵니다. 원칙적으로 무기 고체 전해질도 압출이 가능하지만, 경도 증가와 낮은 가공성, 용매 없이 얇고 균일한 필름을 생산해야하는 기술적 문제를 해결해야합니다. 산화물 전해질의 경우에는 소결을 해야한다는 문제도 있습니다.
건식 압출법외에도 양극제조에 연구되고 있는 건식 처리 방식인 “건식 캘린더링”, “건식 분사 (Spray)”, “스크린 프린팅”과 같은 방법을 고체 전해질 분리막 생산에도 적용될 수 있습니다.
분말 기반 공정 (Powder-based processing)
산화물 전해질의 경우, 고온 소결을 제거하거나 온도를 크게 낮추기 위한 대체 생산 방법이 연구되고 있습니다. 이러한 방법중 하나로 제시되고 있는 것이 에어로졸 증착 (Aerosol deposition: AD)을 사용하는 분말 기반 공정입니다.
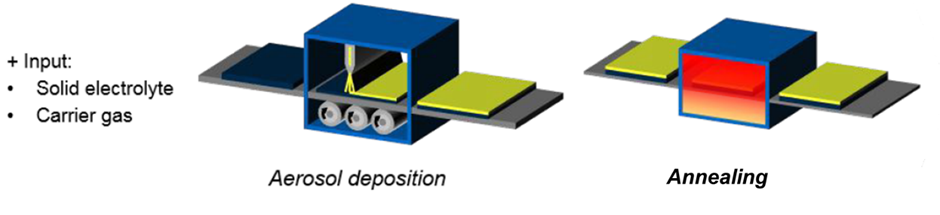
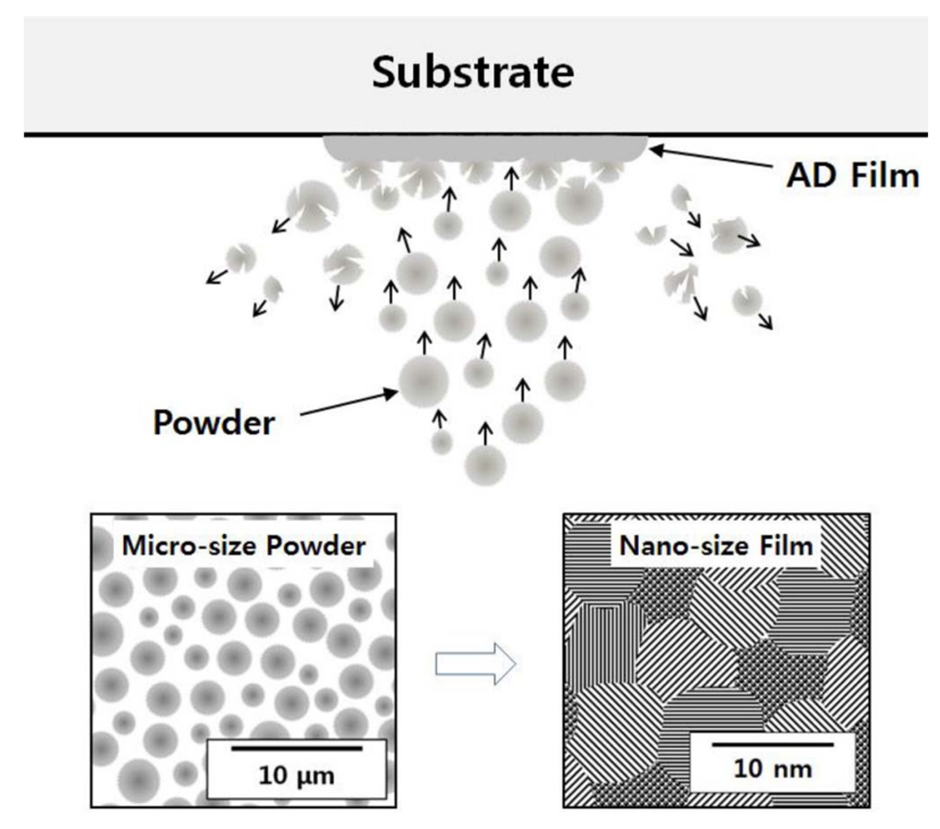
이 기술에서는 운반 가스로 사용되는 질소나 아르곤이 고체 전해질 분말과 함께 에어로졸을 형성하여 기판으로 운반됩니다. 운반 가스는 에어로졸 챔버에서 진공 증착 챔버로 고체 전해질을 운반하여 이를 양극에 증착합니다. 에어로졸 챔버와 증착 챔버 간의 압력 차이로 인해 강한 접착력과 밀집된 층 형성이 가능합니다. 더 밀집된 층을 얻기 위해 600°C에서 어닐링(열처리) 단계를 거치며, 고온 소결 단계를 완전히 생략할 수 있어 원치 않는 부반응도 방지됩니다. 에어로졸 증착은 조밀하고 얇은 필름(1–100 μm)을 가능하게 하며, 용매가 필요하지 않습니다. 그러나 이 기술은 새로운 기술로, 진공 상태에서 작동해야 하므로 비용이 많이 들며 현재 약 10 mm³/분의 증착 속도를 다른 제조방법과 경쟁하려면 1000 mm³/분 이상으로 올려야 합니다. 따라서 당장 대량의 고체 전해질을 생산하는데 사용하기는 어려우며 현재 이 기술을 도입할수 있는 영역은 양극에 매우 얇은 고체 전해질 코팅을 증착하는 것입니다.
대량 고체 전해질 생산에서는 에어로졸 증착이 아직까지는 압출 또는 습식 처리 기술과 경쟁할 수 없지만, 산화물 전해질 제조에 많은 장점이 있기 때문에 많은 회사들이 여전히 이를 제조 로드맵에 포함하고 있습니다.
출처: Solid-State Battery Roadmap 2035+ (Fraunhofer ISI report)
'배터리 > 전고체 배터리 (All Solid State Battery)' 카테고리의 다른 글
전고체 배터리 전망_제조공정_음극 (1) | 2024.09.11 |
---|---|
전고체 배터리 전망_제조공정_양극 (5) | 2024.09.10 |
전고체 배터리 전망_구성요소간 호환성 (2) | 2023.12.08 |
전고체 배터리 전망_할로겐화물 및 붕산염 고체 전해질 (1) | 2023.12.07 |
전고체 배터리 전망_폴리머 고체 전해질 (1) | 2023.11.17 |