2025. 3. 12. 23:18ㆍ배터리/배터리 제조
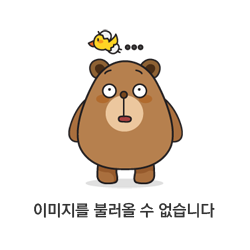
기가팩토리 규모 배터리 생산의 현황과 도전 과제 (STATUS QUO AND CHALLENGES IN GIGA-SCALE BATTERY PRODUCTION)
빠르게 성장하는 배터리 시장 (THE BATTERY MARKET IS GROWING RAPIDLY)
기후 목표 달성을 위해 교통 부문(전 세계 온실가스 배출량의 약 20%)은 에너지 부문(약 30%)과 함께 가장 중요한 영향을 미치는 분야 중 하나입니다. 이에 따라 전동화 및 재생 가능 에너지원으로의 전환이 핵심적인 해결책으로 부각되고 있으며, 두 분야 모두 배터리 시스템을 활용한 에너지 저장 및 공급이 필수적입니다.
이러한 흐름 속에서 배터리의 글로벌 수요는 최근 몇 년간 급격히 증가하였습니다. 이는 주로 전기 승용차 및 고정형 에너지 저장 시스템의 급성장에 의해 주도되고 있으며, 소형 휴대용 전자기기에서도 배터리 사용이 확대되고 있습니다.
이와 같은 전동화 트렌드는 상용차 부문에서도 빠르게 확산되고 있으며, 모든 공개된 시장 전망에 따르면 배터리 수요는 향후 지속적으로 강한 성장세를 보일 것으로 예상됩니다.
Figure 1을 보면 2023년 배터리 수요는 약 5,000GWh에 이를 것으로 전망되며, 이는 연평균 34%의 성장률에 해당합니다. 이러한 전기 에너지 저장 수요를 충족하기 위해 대규모 배터리 공장(기가팩토리)이 전 세계적으로 다수 계획되고 있으며, 건설이 진행 중입니다.
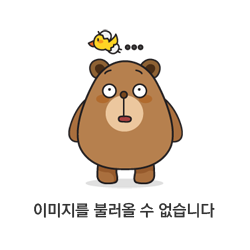
배터리 생산 공정 개요 (BATTERY PRODUCTION AT A GLANCE)
배터리 셀 제조 공정은 셀의 형식에 따라 다소 차이가 있지만, 일반적으로 세 가지 주요 단계로 나뉩니다: 전극 제조, 셀 조립, 셀 마감입니다.
- 전극 제조: 활성 물질을 바인더, 전도성 첨가제, 용매와 혼합하여 슬러리를 제조한 후, 이를 얇은 금속 박막(집전체)에 코팅하여 양극과 음극을 제작합니다. 이후 건조 및 압착 공정을 거쳐 전극을 완성합니다.
- 셀 조립: 제조된 전극을 분리막 및 전해질과 결합하여 개별 배터리 셀을 형성합니다.
- 셀 마감: 초기 충·방전 과정을 통해 셀을 전기화학적으로 활성화합니다.
특히 전극 제조 단계에서는 공정 변수 간의 복잡한 인과관계가 존재하며, 대량 생산을 위한 스케일업 과정에서 많은 기술적 도전 과제가 발생합니다. 따라서 이 단계에서는 다학제적인 협력이 필수적입니다.
기가팩토리 배터리 생산이 직면한 주요 과제 (GIGA-SCALE BATTERY PRODUCTION FACES MANY CHALLENGES)
셀 설계 및 소재 선택과 무관하게, 제조 공정은 배터리 셀의 성능, 안전성, 지속 가능성 및 비용에 막대한 영향을 미칩니다.
기가팩토리 규모의 대량 생산은 규모의 경제를 통해 비용 절감 효과를 기대할 수 있지만, 원자재 조달, 물류, 에너지 소비 및 품질 관리 측면에서 심각한 도전 과제를 수반합니다.
배터리 생산 공정은 여러 개의 연속적인 제조 단계를 포함하며, 각 공정 간의 복잡하고 민감한 상호 의존성이 존재합니다. 이로 인해 공정 조건(window)을 유지하는 것이 매우 어려우며, 미세한 편차가 제품 품질에 큰 영향을 미칠 수 있습니다.
또한, 공정별 조정 가능한 매개변수(parameter)의 수가 많아, 기존의 시험과 오류(trial-and-error) 방식으로는 최적의 공정 전략을 수립하기 어려운 실정입니다. 그 결과, 10% 이상의 높은 불량률이 발생하는 경우도 흔치 않습니다.
특히 생산 램프업(ramp-up) 단계는 배터리 제조에서 가장 중요한 과정 중 하나입니다. 이 단계에서는 매우 높은 운영 비용이 발생하는 반면, 생산성과 매출은 거의 존재하지 않는 상태에서 시작합니다.
공정 안정성이 확보되지 않은 상태에서는 목표한 품질 수준을 달성할 수 있는 최적의 공정 조건을 찾는 것이 어려워지며, 이로 인해 램프업 기간이 몇 달 이상 지속될 수도 있습니다.
또한, 이 과정에서는 대량의 원자재가 투입되기 때문에 초기 비용이 높고, 환경적 부담도 증가합니다.
이러한 문제를 해결하기 위해 데이터 기반 최적화(data-driven optimization)가 유망한 해결책으로 주목받고 있습니다.
핵심적인 접근 방식은 측정 데이터의 시계열(time-series) 패턴을 분석하고, 인공지능(AI) 알고리즘을 활용하여 미래의 변화를 예측하는 것입니다.
최근 AI, 머신러닝 알고리즘, 그리고 연산 성능의 발전은 실시간 데이터 분석 및 공정 최적화를 가능하게 하였으며, 이를 통해 불량률 감소(scrap reduction) 및 품질 향상이 가능해졌습니다.
제조 산업에서 AI가 야심찬 목표를 현실로 만들다 (AI IN PRODUCTION MAKES AMBITIOUS TARGETS FEASIBLE)
제조 산업에서의 인공지능(AI) 활용은 1980년대 후반부터 본격적으로 시작되었습니다. 초기에는 분류 및 조립 같은 단순 작업을 자동화하여 생산성을 향상하는 데 집중되었습니다.
1990년대에는 보다 정교한 알고리즘과 고급 제어 시스템이 도입되면서, 의사 결정 최적화 및 기계의 적응성이 향상되었고, 운영 비용이 절감되었습니다.
21세기에 들어 AI의 역할은 더욱 확대되어 예측 분석(predictive analytics)을 통해 축적된 데이터를 기반으로 유용한 인사이트를 도출하는 데 활용되고 있습니다.
이러한 데이터 기반 접근법은 공정 운영을 최적화하고, 품질 및 안전성 기준을 유지하는 데 기여하고 있습니다.
현재, AI가 제조업에 미치는 영향은 혁신적이라 할 수 있습니다.
실시간 머신러닝 기술이 생산 공정에 적용되면서, 공장에서 AI 기반 로봇, 센서, 비전 시스템으로부터 실시간 데이터를 수집하여 보다 신속하고 정밀한 의사 결정을 내릴 수 있게 되었습니다.
이로 인해 수작업에 대한 의존도가 낮아지고, 운영 효율성이 향상되며, 운영 비용이 크게 절감되는 효과가 나타나고 있습니다.
과거에는 SF적인 개념으로 여겨졌던 AI 기반 제조 혁신이 이제는 현실화되었으며, 산업 전반에 걸쳐 제조 방식을 근본적으로 변화시키고 있습니다.
AI의 변혁적 힘은 제조업을 전례 없는 수준의 효율성과 혁신으로 이끌고 있으며, 기가팩토리를 포함한 대규모 생산시설에서 지속 가능한 미래를 가능하게 하는 핵심 요소로 자리 잡고 있습니다.
출처: MAXIMIZING EFFICIENCY: NAVIGATING THE GIGAFACTORY JOURNEY WITH REAL TIME DATA INSIGHTS
'배터리 > 배터리 제조' 카테고리의 다른 글
미래의 배터리 셀 공장: 자동화, AI, 공정 개선을 통한 비용 절감과 효율성 극대화 (2) | 2025.03.01 |
---|---|
유럽 배터리 산업의 위기와 해결 방안 (1) | 2024.12.16 |
전기차 배터리 가격 2026년까지 50% 가까이 하락 예상 (8) | 2024.11.07 |
한국 배터리 제조 설비 업체 현황-물류 및 검사 공정 (0) | 2022.10.11 |
한국 배터리 제조 설비 업체 현황-화성 공정 (2) | 2022.10.10 |